Definition Of Welding – Right now, humanity is striving towards wonder, every single day we keep increasing the height of the peak of our advancement. New technology is discovered every day and it helps us build so many things on a microscopic scale to megastructure. In terms of the megastructure, welding is one of its foundations.
Every time you enjoy seeing a skyscraper, passing through a bridge or tunnel, and living in a 100 storied building, it’s all made possible by welding technology. So what is welding? Why is it so important for our development? Discover it all by finishing this article.
Definition Of Welding:
Welding is one of the methods to join two pieces (sometimes more) of metal together. Basically, there are 3 methods of joining metal, by mechanical fastening, adhesive bonding, and welding. They’re all distinguished by how the metal is joined.
In welding, the two pieces of metal called base metal is melted into entering liquid phase along with filler metal (in most cases while in some cases filler metal is optional) and the mix of the two base metal and the filler metal solidify (this mix is called weld metal) becoming a welded joint that connects the two pieces of base metal.
The further classification of welding is classified under how the metal is melted. If it’s melted by the heat generated from electric arc, it’s called arc welding (e.g. SMAW, GMAW, TIG), which is the most common welding method nowadays. If some pressure is utilized during welding, it’s called resistance welding (e.g. ERW, FSW, Spot Welding), usually being done in the workshop because of its machine immobility.
Gas welding, a welding process that requires burning fuel to generate heat (e.g. Oxy-Acetylene Welding). A welding process that involves chemical reaction to produce heat (e.g. thermite welding). So many processes that have the same goal, which is to produce enough heat required to melt the metal. Because welding is defined as a process of melting part of metal pieces before solidifying and become a weld joint.
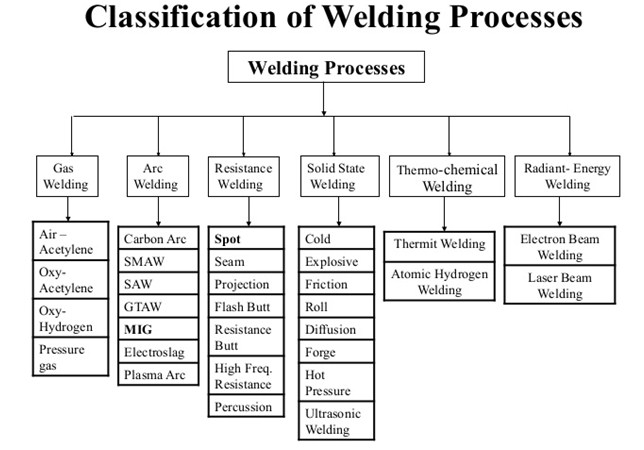
History Of Welding
The art of joining two pieces of metal together has existed long before modern days. Although the method is very different, for example, how medieval people used to forge a sword which is basically red-hot pieces of metal smashed with a hammer and the force will create bonding between metal pieces.
The development of arc welding started in the 1800s when Sir Humphry Davy first discovered an electric arc. Which is then developed by Vasily Petrov into a more stable and continuous form? In the early 1900s inventor, Nikolai Benardos and Stanislaw Olszewski developed the first arc welding method using carbon electrode called carbon arc welding before improved by Nikolai Slavyanov and C. L. Coffin with the use of the metal electrode. Until finally A. P. Strohmenger invented a coated metal electrode (flux) that provide a more stable arc.
Another method of welding also developed during the same period. In the late 1800s and early 1900s methods like resistance welding, thermite welding, and oxy-acetylene welding began to develop. The first recorded patent of resistance welding dated back to 1885 which belong to Elihu Thomson.
Thermite welding started to develop in 1893. Although Edmund Davy discovered acetylene in 1836, the welding torch suitable for the welding process only started to develop in the 1900s, making oxy-acetylene welding very popular during that period due to its low cost and portable nature. Until the development of flux in metal electrode made arc welding become more favorable for producing industrial standard weld joint.
The event of the World War also plays an important role in boosting the development of welding technology. Every nation’s military forces were racing against each other to produce the best weld joint. During this time, joint quality improved so much as well as productivity. The introduction of the semi-automatic process where filler metal is continuously fed to the molten weld pool is a breakthrough that significantly increases productivity.
Later on, in 1930 inventor Kyle Taylor invented stud welding that gained popularity in shipbuilding and construction. Submerged arc welding is also developed around the same year stud welding being invented. Konstantin Khrenov successfully welds underwater in 1932, a method that’s still being implemented even today.
Later on, GTAW (Gas Tungsten Arc Welding) and GMAW (Gas Metal Arc Welding) are invented in 1941 and 1948 respectively, allowing much other metal variation to be welded with improved quality. Shielded metal arc welding (SMAW) is developed in the 1950s and quickly become a popular welding method. Flux-cored arc welding started to develop much later in 1957 together with plasma arc welding.
See: Tungsten Inert Gas Processes And Equipment
Welding Technology
Today, welding has developed so much, it became versatile and highly efficient. Various material, especially the one which has low weldability can be easily welded with today’s technology. The development of electric circuit and the electric instrument also contribute significant advancement of welding, especially in term of arc welding. We can now harness almost the full potential of electric energy.
Allowing us to create a welding machine with many useful features and also powerful (high duty cycle). Examples of those features such as the hot start feature that’s common in SMAW, allowing welders to ignite an electric arc easier due to voltage jump during ignition that returned to normal when the welder start welding.
Another example is pulsating alternating current technology in GMAW, FCAW, and GTAW. This technology is very useful when dealing with material that can’t take too much heat such as aluminum or thin material in general.
Material science and chemistry that play a vital role in welding is also developing and in turn, contributed to improving welding technology. The discovery of material properties helps welding engineers to correctly set the parameter for achieving high-quality weld joint. Coupled with an improved understanding of chemistry, welding engineers can easily set multiple key factors that can affect the quality of the weld before even starting to weld.
For example, when creating a WPS (Welding Procedure Specification) of a material, say aluminum, it’s requested that the aluminum shall be weld by GTAW. Now the engineer can easily decide the fitting electrode, filler metal, shielding gas, and the required heat treatment to achieve the desired quality.
Thanks to material science and chemistry, there are many welding consumables that can help ease the welder’s job, such as anti-spatter chemical that prevents spatter sticking on the surface of the material, aluminum oxide layer removal that’s highly useful before welding aluminum.
Welding machine also becomes more effective and efficient. As electrical component becomes smaller and smaller, so does welding machine. Now exist various welding machines with different capacities in various size. This makes welding become mobile, can easily reach any spot. Automated welding is also starting to rise as of now. Letting the machine do all the work for humans by the touch of a finger.
See: Stick Welding Machine Parts
The Challenge For Future Welding Technology
Right now humanity should aim for sustainability instead of blindly creating things that will potentially endanger human existence itself. Welding is a process that uses a tremendous amount of energy. An amount that we someday won’t be able to provide. Furthermore, welding is costly to nature.
So the concern should be shifted to creating a welding method with high efficiency and also eco-friendly. The latest development proves that a low cost and clean welding method is not utopic. We’re actually already heading that way. The question remains on how fast we can get to the point where welding is cheap and environmentally friendly.
Take the rise of automated welding for example. Automation technology has been around for just a few decades. Though automated welding is already here, it’s still in its infant stage, we still need more time to fully develop a functionally automated welding. Though we’re heading to the correct way, we’re still not fast enough. The existence of automated technology in general and automated welding specifically will be a game-changer that will revolutionize the industry.
It’s a controversial subject, but we should admit that when the machine is taking over, so many things will be improved greatly. The factor of human error can be greatly diminished thus increasing work efficiency in general.
Not including humans in the welding environment can also save millions of lives from the danger of welding itself. As there are many welding-related health issue that can be prevented if we just exclude humans from the equation. So in a way, automated welding will also contribute to creating a better environment.
Another important issue to be noted is the development of material science on which welding should also be able to keep up. In short, welding technology should improve as fast as material science develop, therefore welding can stay relevant and reliable method for joining metal.